Predictive is more productive – take the guesswork out of maintenance
If you like thrills and twists in your maintenance schedule, click away now. Johnson Controls predictive maintenance takes the drama out of optimizing equipment performance. Less downtime. Fewer surprises. Banish mystery failures. Just boring, reliable uptime.
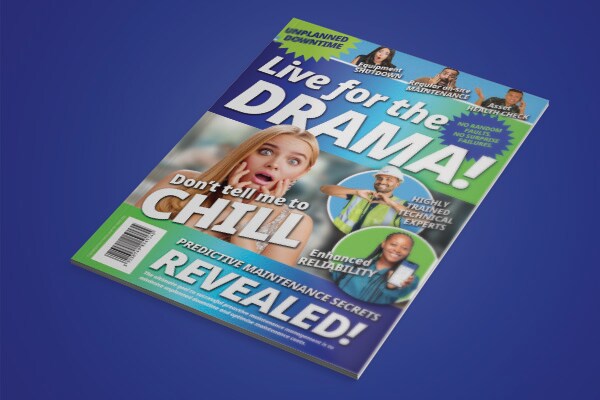
Service is a critical piece of the building lifecycle equation. Regular wellness checks and maintenance are essential so we can function at our best and lead the longest life possible.
Building equipment, such as heat pumps, chillers, fire safety equipment or building automation systems, is not only imperative to the performance and longevity of a building, but also to bottom line costs. When investing in new equipment for a retrofit or a new build, we encourage customers to think about the entire lifecycle of their equipment right from the outset.
Using AI, OpenBlue service experts can detect chiller faults up to 48 hours before they become problems, and failures with 82% accuracy.
- Going beyond “break-fix”
Today’s complex facilities need experienced operators watching over the building, identifying issues and correcting problems before they impact occupants or operations. By moving from a reactive to a predictive model, experts can detect problems before they occur, ensuring business continuity and saving costs. At Johnson Controls, we have invested in a digital infrastructure with a growing number of remote operating centers around the world that continuously monitor our customers’ facilities. Teams of expert technical engineers proactively analyze building data, conducting daily health checks and providing technical assistance. If inefficiencies are found, we can generally fix around 60% of problems remotely.
- Digitalization is a game changer
Digital services help you meet your operational, financial and sustainability goals. Using digitally enabled, tailored solutions, we’ll help you identify, prioritize and implement changes that increase efficiency, minimize unplanned downtime, reduce energy consumption and deliver a healthier environment for occupants. Why not start by optimizing your chiller’s performance? Chiller systems can consume as much as 40% of your building’s total energy costs, so it’s no surprise that many building owners and operators are now thinking about chiller optimization. What’s not to like about reducing your chiller system’s downtime by as much as 50%, lowering your system energy costs by up to 20% and benefiting from a lower cost of ownership
- Predictive is more productive
The ultimate goal to successful, proactive maintenance management is to minimize unplanned downtime and optimize maintenance costs. This is where predictive maintenance comes in.
With the use of AI and predictive diagnostics, technicians will know what needs to be done more quickly, rather than spending hours trying to figure it out, allowing them to be more productive with other tasks. This is significant when you consider the increasing shortage of direct labor in the field: For every eight industry retirements, only one new technician enters the workforce.
The sooner you start maintaining the technology, the better the performance, efficiency and reliability of the equipment - and the longer the lifecycle. Learn more about digital services here.