Smart and connected: advanced sensors enhance A2L refrigerant safety
PENN System 550 utilizes the fastest responding A2L refrigerant leak sensors on the market.
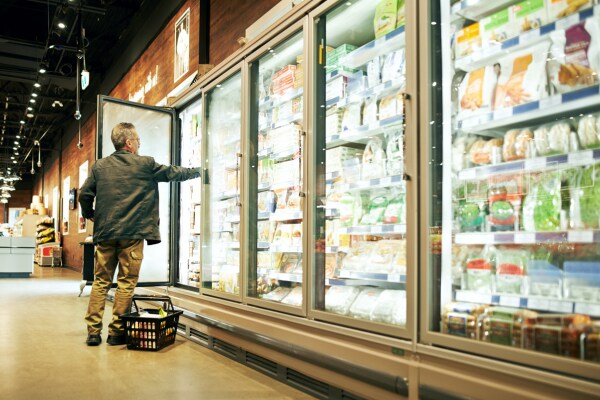
By Keith Gifford, Global Product Manager and Bill Merritt, Director of Business Development
The transition to low-global warming potential (low-GWP) refrigerants has advanced rapidly and is expected to make a significant environmental impact. However, the transition has left many system engineers and building operators under immense pressure to ensure that any newly installed HVACR equipment complies with refrigerant regulations and safety standards. As the hydrofluorocarbon (HFC) phasedown continues, alternative refrigerant options have been introduced that require significantly different safety protocols.1
Today’s low-GWP refrigerants primarily fall into ASHRAE refrigerant classifications A1, A2L and A3. Because of the increased flammability of A2L and A3 refrigerants.2 The EPA now requires certain A2L-based HVACR equipment to include refrigerant leak detection systems (RLDS).
RLDS systems, such as the PENN® System 550 control and GM200 series A2L sensors from Johnson Controls, detects A2L refrigerant leaks and activates a mitigation scheme to prevent leaked refrigerant from reaching concentrations greater than 25% LFL (lower flammability limit). Refrigerant mitigation strategies vary based on equipment but typically involve turning on evaporator fans, closing isolation valves (to prevent additional refrigerant loss), and turning off the compressor until the concentration of leaked refrigerant is below the required limit.
As refrigerant requirements continue to evolve, future-ready leak detection systems that leverage smart sensors and two-way cloud communications can help to ensure safe, compliant and productive operations, delivering value and peace of mind for years to come.
For building owners and operators, this means available RLDS technologies must be considered if the goal is to optimize equipment uptime. Refrigerant leak detection technology designed around smart sensors and cloud-connected communications is essential to achieving these goals.
Advancements in refrigerant leak sensors
Reliable and accurate refrigerant leak detection requires advanced sensor capabilities. For instance, PENN System 550 utilizes the fastest responding A2L refrigerant leak sensors on the market. The refrigerant leak sensors leverage speed-of-sound technology to deliver unmatched accuracy and response time. Using a hydrophobic screen and state-of-the-art sensing chamber, the presence of refrigerant disrupts the soundwave profile and initiates alarms when refrigerant concentrations reach a factory set LFL trip point.
Smart RLDS sensors like PENN GM200 series also monitor environmental conditions such as temperature and humidity that have a direct impact on their performance. GM200 series sensors use temperature and humidity baseline measurements to continuously self-recalibrate in order to maintain consistent, reliable performance without operator intervention.
Improving safety with data
Smart sensors can deliver advanced data that allows HVACR systems to be up and running quickly if a refrigerant leak is detected or if there’s a problem with the sensor. Some controllers, including the PENN System 550, combine Modbus communications with remote cloud-based connectivity to maximize uptime and streamline operations. Users can access system alerts, troubleshooting and diagnostic information from a smartphone or connected device. If more than one A2L sensor is installed, the controller identifies which A2L sensor detected the leak, allowing technicians to arrive on-site with the information necessary to act quickly.
Multiple System 550 controllers and their respective sensors (i.e., temperature, humidity, pressure and/or A2L refrigerant sensors) can be viewed on a single cloud-based dashboard. Data from the sensors can be used to determine system health and create strategies to streamline operations, including scheduling predictive maintenance and, setting alerts to monitor sensor lifespan.
Simplifying safety and compliance
Transitioning to low-GWP refrigerants can be a challenge. To ease the transition, it’s important that RLDS systems be easy to install and able to adapt to meet current and future needs as regulations continue to evolve.
Modular, plug-and-play solutions like System 550 can simplify installation and be configured for specific application requirements. For instance, System 550 allows up to six A2L sensors to be connected to a C550CCN control module, as well as up to 10 relay and/or analog outputs through plug-in expansion modules, without the need for field wiring. It is also compatible with sensors for detecting A3 refrigerant leaks (e.g., R290, propane) in preparation for possible future regulations.
As refrigerant requirements continue to evolve, future-ready leak detection systems that leverage smart sensors and two-way cloud communications can help to ensure safe, compliant and productive operations, delivering value and peace of mind for years to come.
------------
1United States Environmental Protection Agency (EPA), “Significant New Alternatives Policy (SNAP)” (June 13, 2024) https://www.epa.gov/snap/regulations-proposed-rules-and-final-rules-determined-epa#rule26.
2American Society of Heating, Refrigerating and Air-Conditioning Engineers (ASHRAE), “Update on New Refrigerants Designations and Safety Classifications” (February 2024) https://www.ashrae.org/file%20library/professional%20development/ashrae-unep/unep---ashrae-factsheet--english-.pdf.